array(8) { ["description"]=> string(796) "Torcon was CM for a renovation and addition program to create a new insulin manufacturing facility in Danbury, CT. Construction was fast-tracked and consisted of a 100,000 sq. ft. new building and 20,000 sq. ft. of renovation. The new facility provides sterile fill and packaging areas, weigh and dispense, and warehousing. The project is designed to house six fill/packaging lines.
The work was completed in three phases: solution prep suite with six process tanks; formulation suite with process vessels and a cryo-granulator; and the fill and packaging area in the new building. The adjacent central utility plant houses three new chillers, three new boilers and two new compressors, plus process utilities (WFI, clean steam, CIP, glacial acetic acid, and waste neutralization).
" ["details"]=> array(3) { ["location"]=> string(20) "Danbury, Connecticut" ["architect"]=> string(21) "CRB Engineers / Kling" ["key_facts"]=> array(3) { [0]=> array(1) { ["text"]=> string(23) "Construction Management" } [1]=> array(1) { ["text"]=> string(16) "120,000 sq. ft. " } [2]=> array(1) { ["text"]=> string(92) "ISPE Facility of the Year Award for the Equipment Innovation and Process Innovation Category" } } } ["featured_image"]=> int(631) ["full_width_images"]=> array(1) { [0]=> int(631) } ["left_column_images"]=> array(4) { [0]=> int(636) [1]=> int(634) [2]=> int(632) [3]=> int(628) } ["right_column_images"]=> array(4) { [0]=> int(635) [1]=> int(633) [2]=> int(629) [3]=> int(630) } ["client"]=> string(20) "MannKind Corporation" ["short_description"]=> string(0) "" }
Technosphere Insulin Manufacturing Facility
Torcon was CM for a renovation and addition program to create a new insulin manufacturing facility in Danbury, CT. Construction was fast-tracked and consisted of a 100,000 sq. ft. new building and 20,000 sq. ft. of renovation. The new facility provides sterile fill and packaging areas, weigh and dispense, and warehousing. The project is designed to house six fill/packaging lines.
The work was completed in three phases: solution prep suite with six process tanks; formulation suite with process vessels and a cryo-granulator; and the fill and packaging area in the new building. The adjacent central utility plant houses three new chillers, three new boilers and two new compressors, plus process utilities (WFI, clean steam, CIP, glacial acetic acid, and waste neutralization).
Project Details
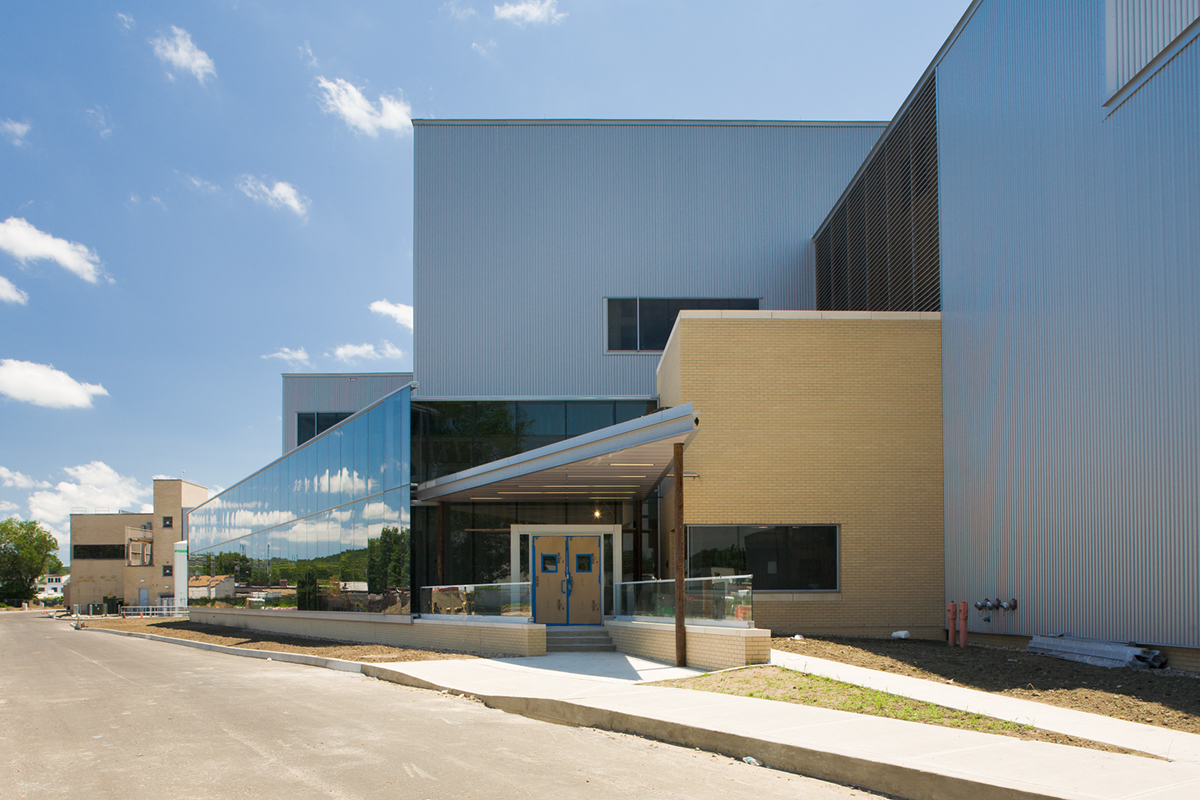
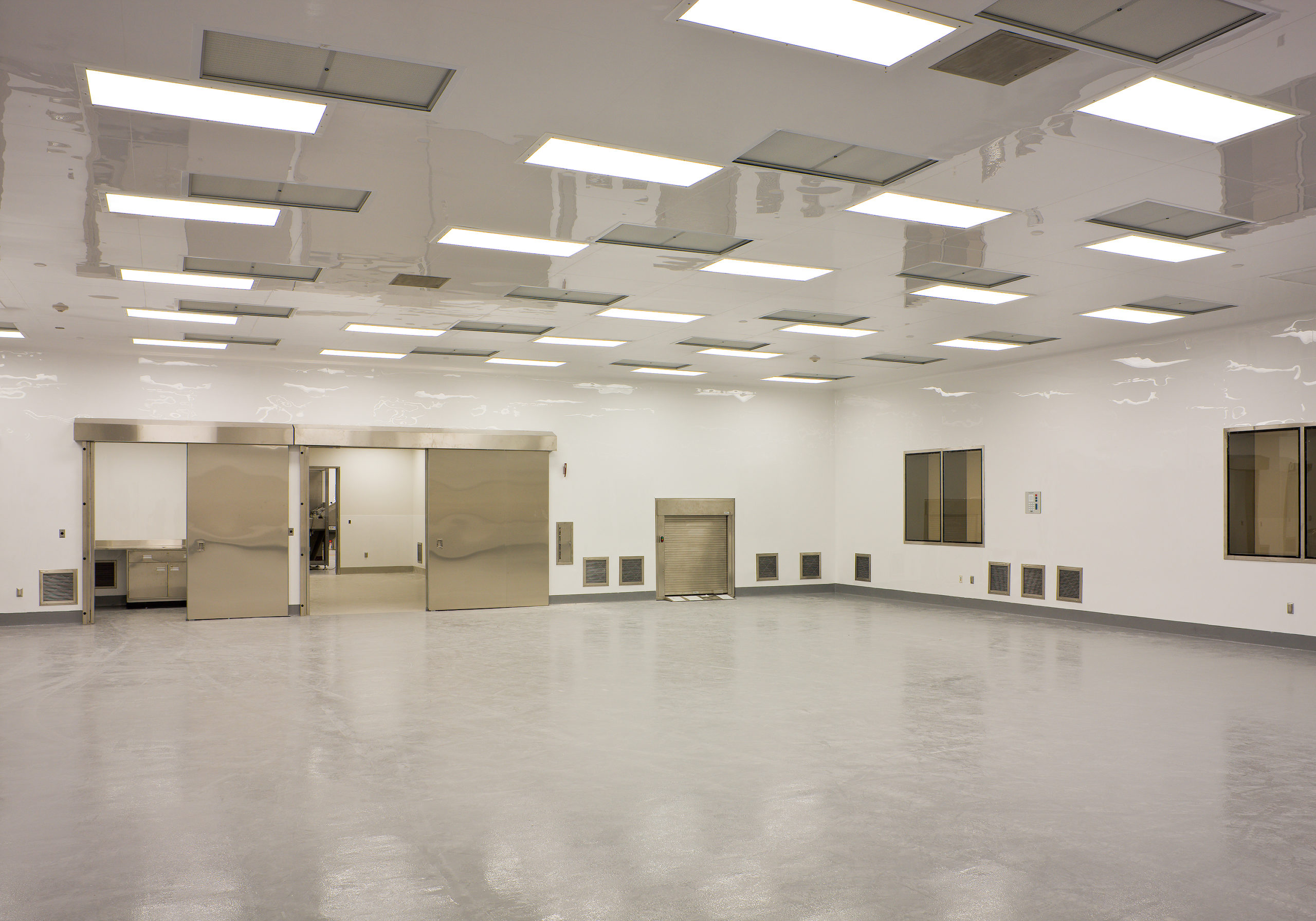
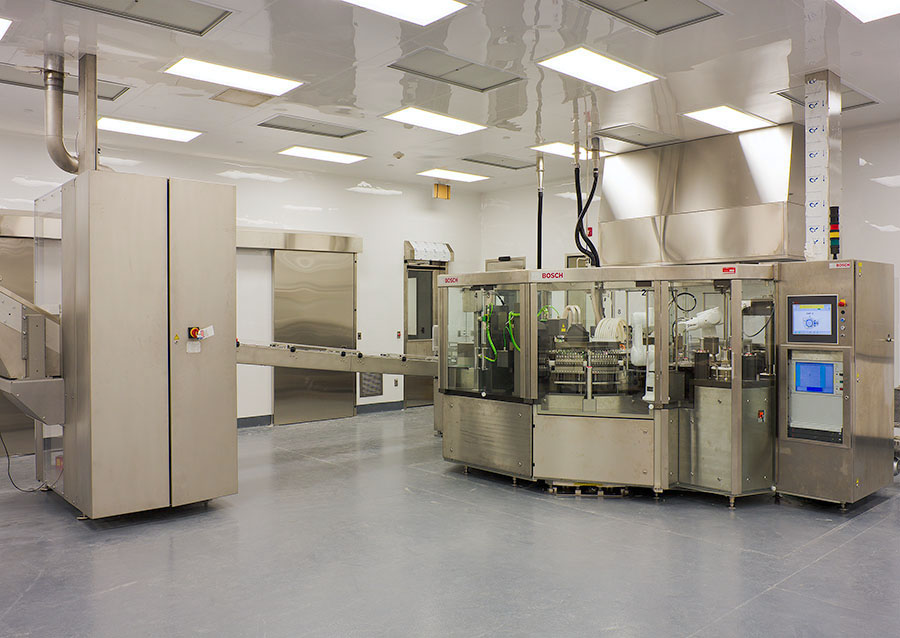
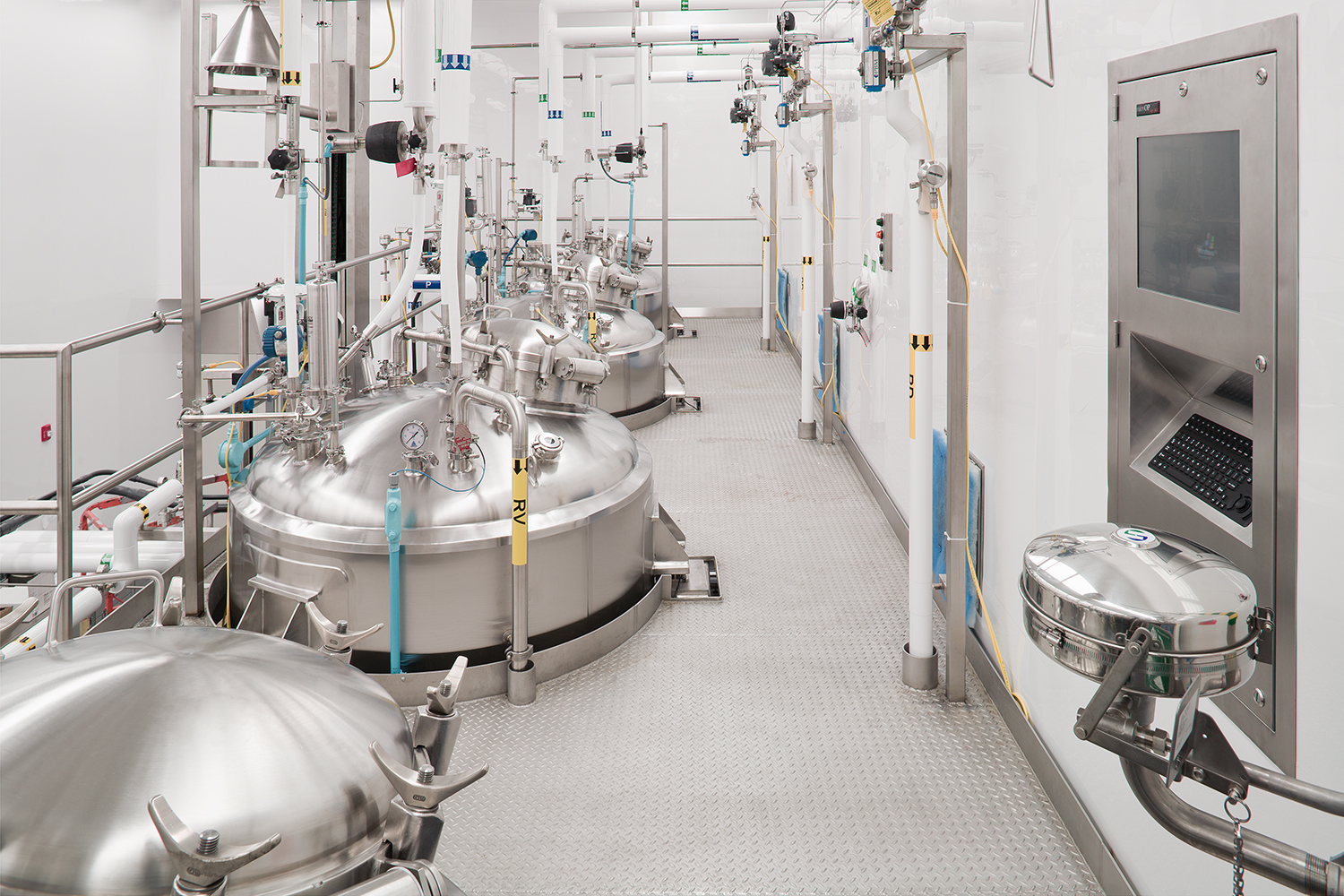
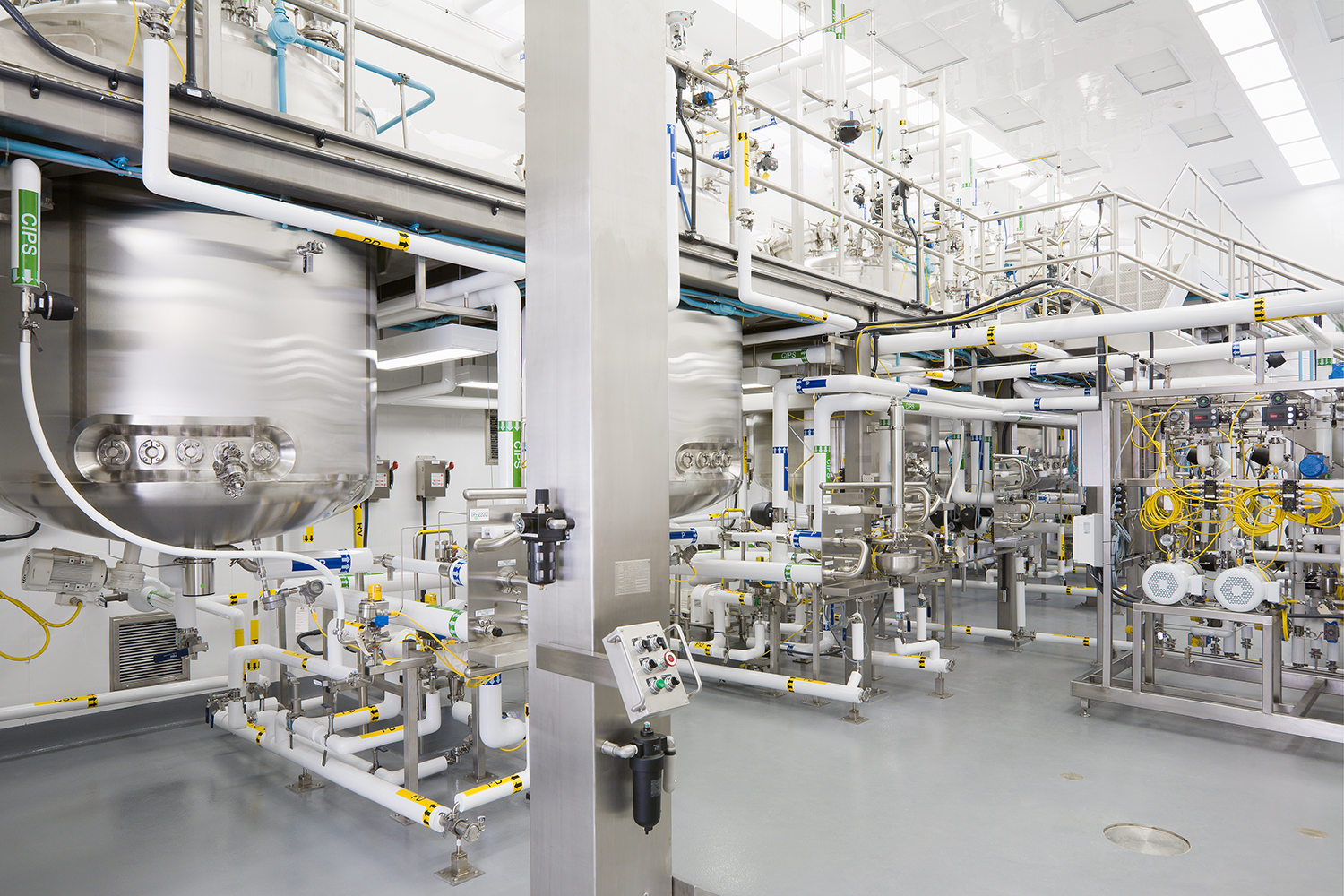
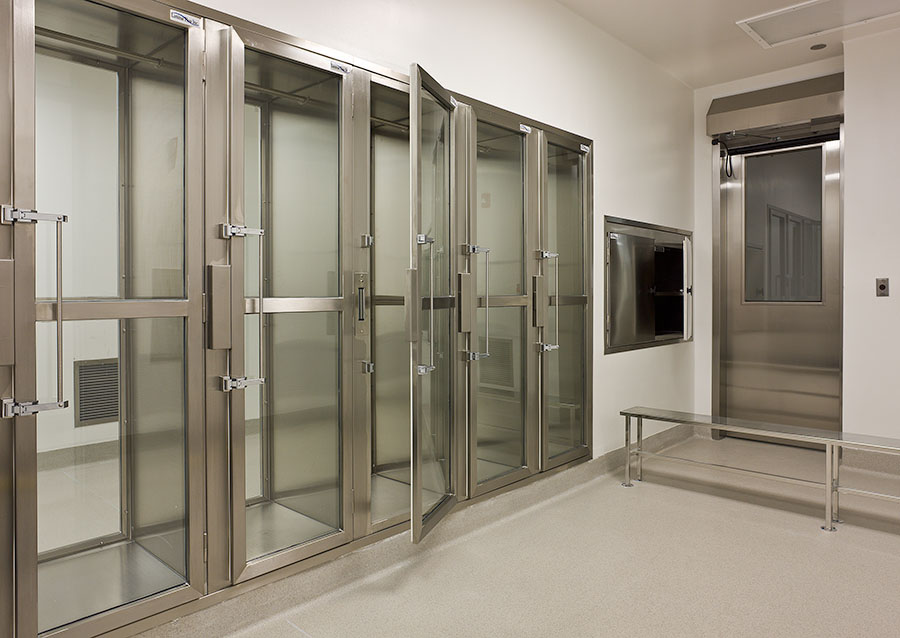
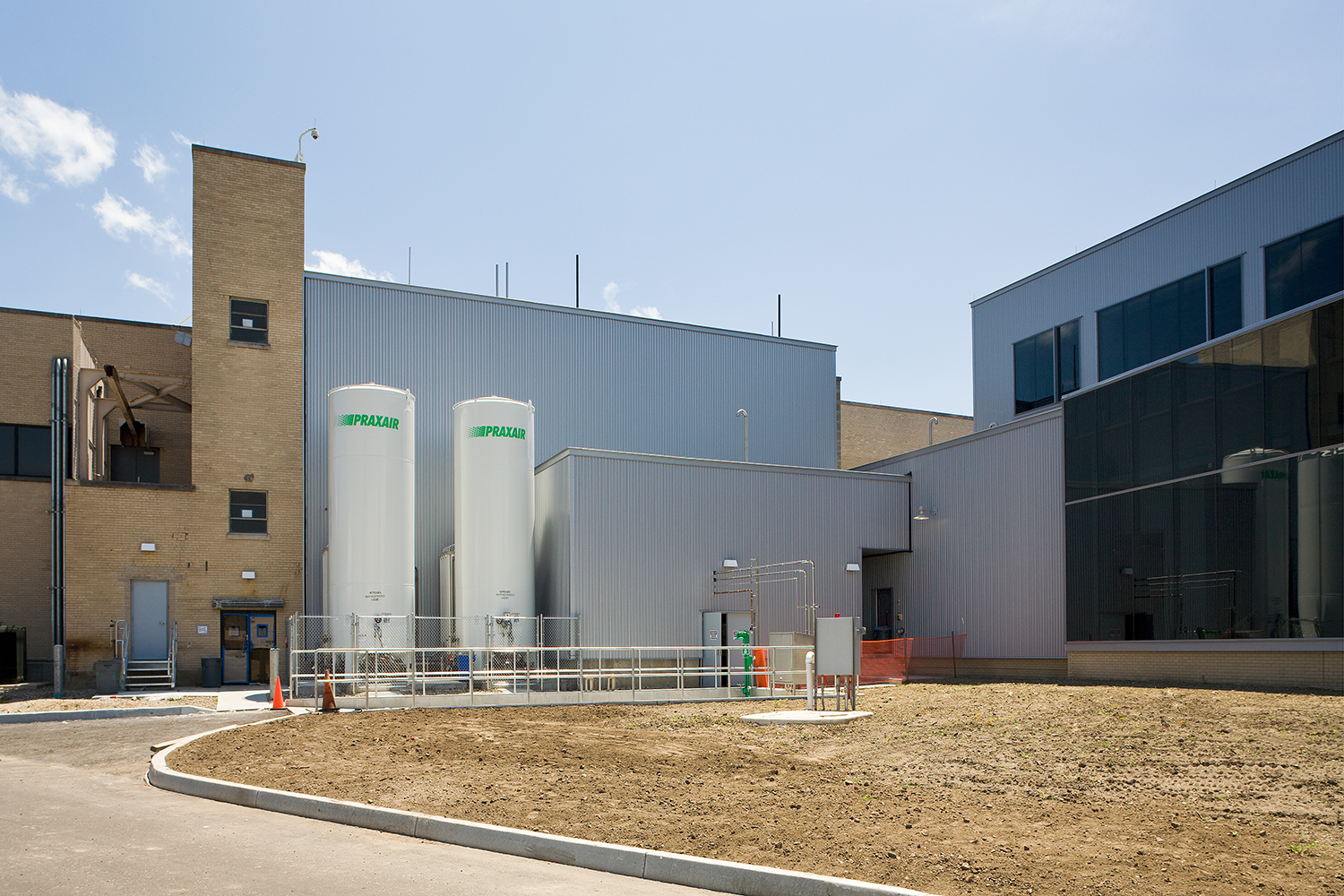
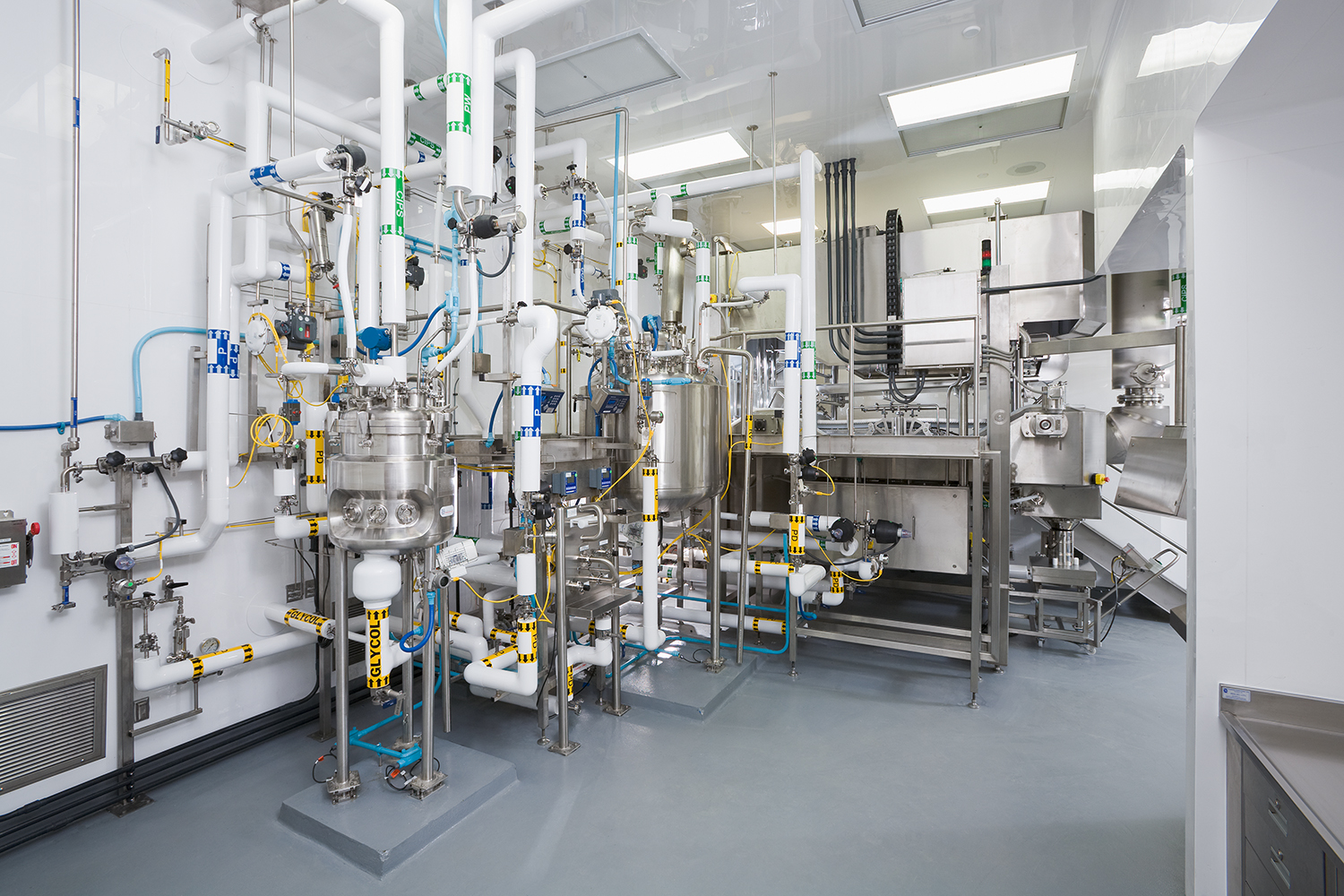
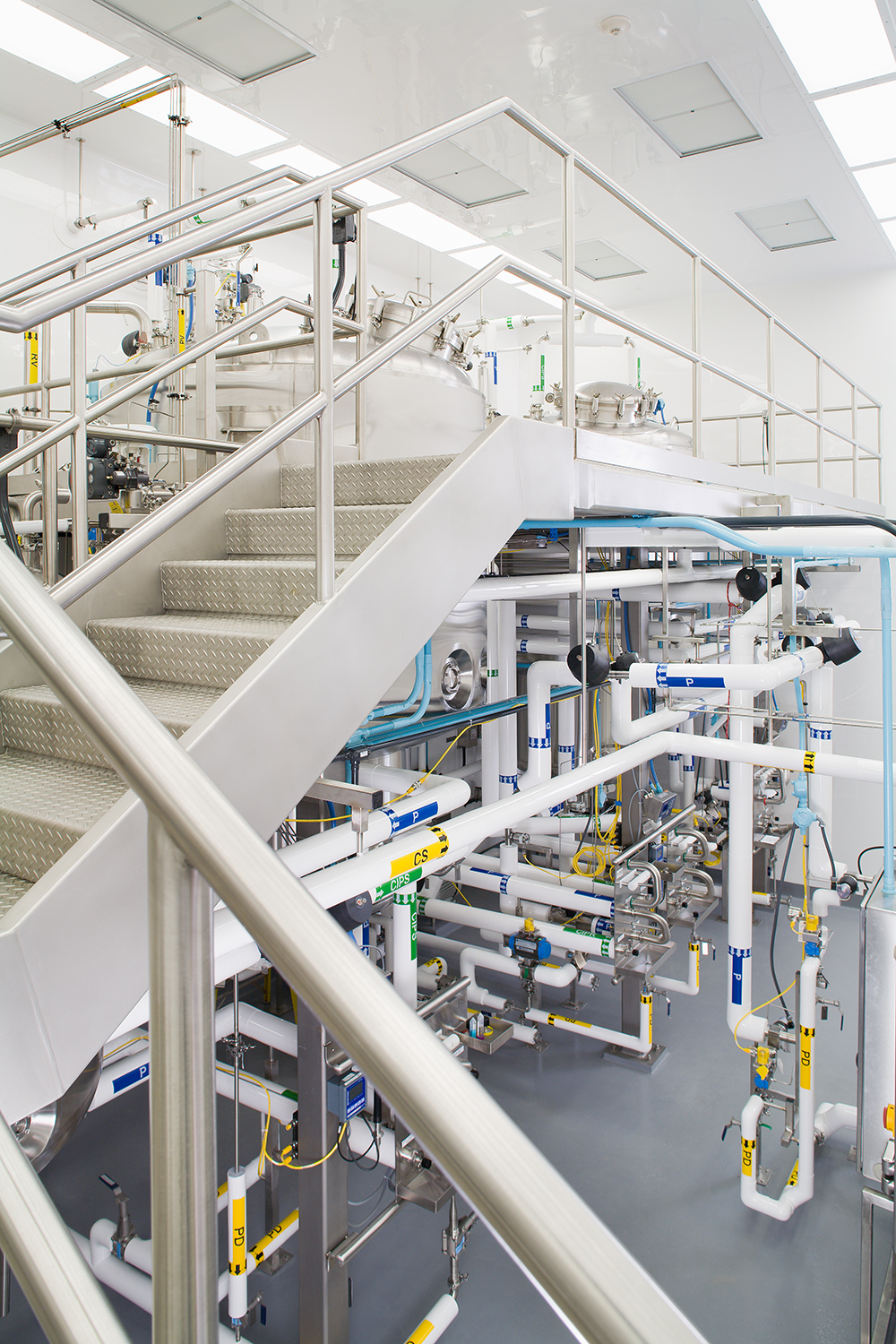